Carving the Mountain
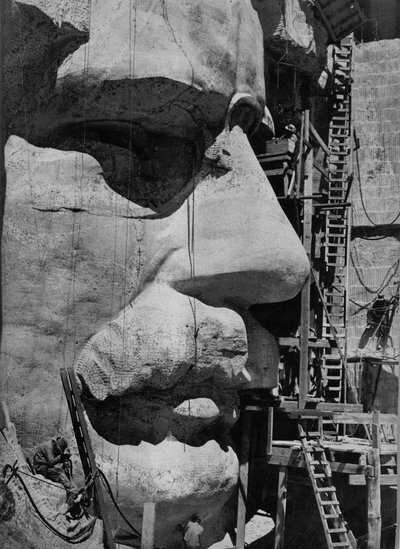
Gutzon Borglum constantly complained that he had to use miners to carve his masterpiece, rather than artists. However, the only experience any living person had with carving mountains into art was Borglum himself, at Stone Mountain in Georgia. Although he did not complete that project, a number of techniques for sculpting Mount Rushmore were developed there.
The infrastructure needed to get to the top of mountain included stairs and a tramway. The stairway had 506 steps and 45 ramps -- the equivalent of a forty-story building. The tramway was originally meant just for transporting tools and supplies, leading from a lower loading house up to an A-framed structure on the top of the hill. Later, to make it safe to carry men, Park Service engineer Julian Spotts strengthened the A-frame and equipped the tramcar with an emergency brake.
The workers were expected to be at the top of the mountain by 7 a.m. in the summer, or 7:30 in fall and winter. Once up top, men would be fitted into leather harnesses designed by Borglum himself, and lowered down the face of the mountain by means of cables attached to hand-cranked winches. Each man would have to walk up or down the face in coordination with the winch operator or else he would be dragged along the mountain face. To help coordinate this vertical movement between the man on the rock and the winch operator, a "call-boy" was positioned where he could see both men and relay the necessary information.
At Stone Mountain, the carving was a shallow relief (although up to three to five feet deep in places) and so a powerful slide projector was developed to transfer an image to the stone. Unfortunately, this method failed, and it certainly never would have worked at Rushmore. To enlarge a three-dimensional model onto a mountain, Borglum devised a simple system, which had been used in ancient Greece, consisting of an angle and two measurements. On the top of the model head he created in the studio, and on the head to be carved on the mountain, a vertical axis was placed. The apparatus looked like a giant propeller atop each head. By measuring the angle, the distance away from the axis, and the distance down from the top, workers called "pointers" could find the spot on the mountain where drilling or blasting would be done, and then paint instructions on the rock for the drillers to follow. To make things easier, Borglum's models were proportioned 1:12 so that inch measurements on the models could be easily converted to feet.
As at Stone Mountain, dynamite was used to blast the rock into a general shape. To control the blasting, sticks of dynamite would be cut down to make smaller charges, up to 70 for one detonation. The drill holes would be filled with these caps and twice a day, at lunch and 4 o'clock (the end of the workday), when all the workmen were off the face of Rushmore, the dynamite was detonated.
The drillers then removed stone to within six inches of the finished surfaces. The drillers carried Chicago-Pneumatic jackhammers, weighing over 75 pounds, with a hose for the compressed air powering the drill. These were not the easiest tools to handle -- especially when hanging in a harness on the side of a mountain. To position the drills correctly, the workers would keep their heels together and toes apart, and rest the drill bit in the V shape of their feet. Drilling horizontally, however, merely enforced Newton's law: an equal and opposite force swung the men away from the rock. In that case, they would first drill two holes at an angle, attach a chain to those holes using steel pins, and then brace themselves against that chain as they drilled. The drill bits didn't last long under these conditions; every few hours, a worker called a "steel nipper" would climb down in a harness to trade the dull bits with fresh ones.
Then the carvers would take over. By drilling a series of shallow holes in a closely-spaced grid, and then removing these grids by drilling obliquely -- a process they called "honeycombing" — the carvers got very close to finished surface. The carvers did the final finishing using smaller handheld pneumatic hammers. The hammers were used to first remove the roughness left by the honeycombs, and then to define nuanced features — wrinkles or pits in the skin — as directed by Gutzon or Lincoln Borglum.
At the end of the day, the men would be covered from head to toe in granite dust. Compressed air hoses would be used to "blow off" as much of the dust as possible — but there was always more.